Students' innovative construction waste solution wins ‘Smart India Hackathon 2023’
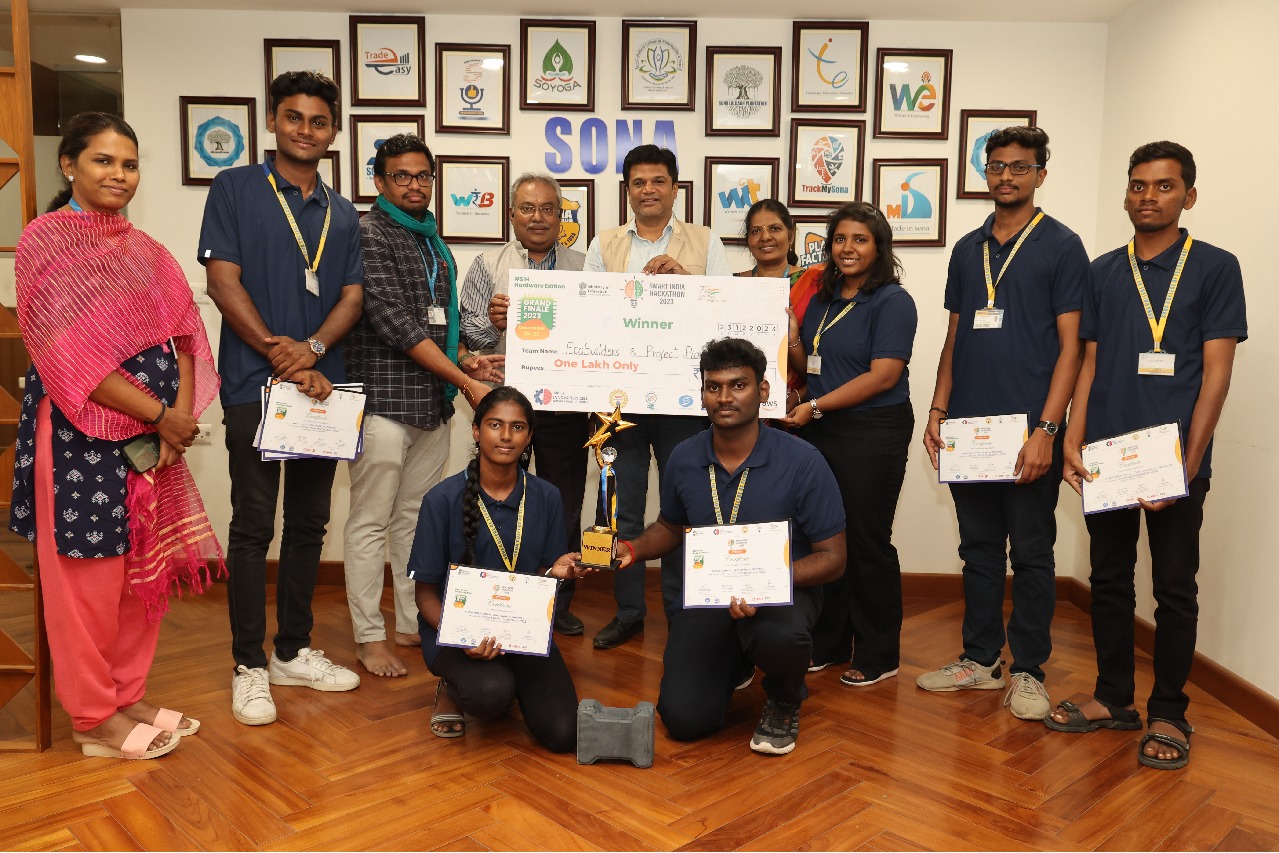
New Delhi, Jan 31 : An innovative solution by students, that aims to address pollution caused by construction and demolition waste generated in the construction industry, has won the top award in the Ministry of Education’s ‘Smart India Hackathon 2023’ national competition.
The civil engineering students from Sona College of Technology in Salem, Tamil Nadu, secured first place in national competition.
Their solution involves utilising construction and demolition waste along with empty plastic cement bags to create robust bricks and paver blocks that can be reused in construction activities.
The team has now won the first prize in the three successive Smart India Hackathons in 2020, 2022, and 2023. (There was no hackathon in 2021.)
The team led by Harshini E K, a final year civil engineering student, had R Mano, Marga Dharshini, Madhuraghavan V, M Hari Prasath, Kirubanithi and Dhinesh Kannan as members.
The team received mentorship from Sona College of Technology Dean of R&D and Professor of Civil Engineering, Dr R Malathy, and Assistant Professor, Dr Karuppasany Narayanan.
"With unwavering commitment and rigour, they pursued a technological solution, simulating industrial conditions in the lab and actively participating in mentoring sessions,” said Dr Malathy.
The students also received a cash award of Rs 100,000.
Working continuously for five days, the team developed a solution demonstrating that construction and demolition waste can be sustainably redeployed on a commercial scale.
The process involved crushing waste, sieving it into coarse and fine aggregates, and adding it to a molten mixture prepared using empty polypropylene bags used for transporting cement.
This molten compound binds the coarse and fine aggregates in paver blocks or bricks.
This unique solution works with all types of construction and demolition waste, regardless of the quality of concrete or materials used, and delivers paver blocks with a significantly better compressive strength than kiln baked mud bricks within three hours.
The team also established that supplying oxygen during the block production process results in higher quantity of carbon dioxide with a purity of 99.99 percent.
This carbon dioxide can be liquefied for commercial use with minimal energy requirements, providing the project with an added sustainable edge.
“Our focus was traditionally on the technical aspects of designing and building structures. However, with Sona Group's commitment to sustainability, our researchers now actively pursue responsible development, with an eye on protecting the environment and making Planet Earth a better place to live," said Chocko Valliappa, Vice Chairman of Sona Group of Institutions.